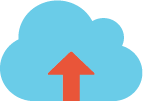
Send
Upload your 3D CAD model
Delivering 100 – 100,000 Parts in as Quickly as 2 Weeks
Get A QuoteSend
Upload your 3D CAD model
Select
Select Your Process & Material
Delivered
Receive Your Parts in Days
At PrintForm, we prioritize customers above all else. Our comprehensive range of industrial advanced manufacturing processes and solutions is designed to meet your unique needs. Instead of focusing on specific technologies or machines, we direct our attention towards serving you with excellence.
PrintForm specializes in injection molding and offers a wide range of capabilities to meet your needs. Our expertise includes:
PrintForm offers over 50 different plastics including fiber filled options, fire retardant, and Silicone Rubber
Find out how PrintForm can help you. Call 404.692.5500 today!
Injection molding is a manufacturing process used to produce plastic parts in large quantities. It involves injecting molten plastic material into a mold cavity, allowing it to cool and solidify, and then ejecting the finished part from the mold. Injection molding is widely used across various industries due to its efficiency, precision, and ability to create complex shapes. It is a cost-effective method for producing high-quality plastic components with consistent dimensions.
An injection molding machine is a specialized device used in the injection molding process. It is designed to melt and inject plastic material into a mold to produce plastic parts. Injection molding machines consist of several key components, including:
Heating Unit: The heating unit, often called the barrel, contains a reciprocating screw or a plunger that heats and melts the plastic material. The heating unit maintains precise temperature control to achieve the desired melt viscosity.
Injection Unit: The injection unit is responsible for injecting the molten plastic material into the mold cavity under high pressure. It consists of a screw or a plunger, which moves forward to push the molten plastic into the mold through a nozzle.
Clamping Unit: The clamping unit ensures the mold remains tightly closed during the injection process. It consists of a movable platen and a stationary platen that hold the mold in place. The clamping unit provides the necessary force to keep the mold closed against the pressure exerted by the injected plastic.
Control System: The control system is the brain of the injection molding machine. It includes a control panel and a computerized control system that allows operators to set and adjust various process parameters, such as injection speed, temperature, pressure, and cycle times.
Injection molding machines vary in size and configuration, ranging from small tabletop machines used for prototyping and small-scale production to large industrial systems capable of producing complex parts with high precision and efficiency.
Injection molding is a versatile manufacturing process that is used across a wide range of industries. It is particularly suitable for producing plastic parts in large quantities with high precision and consistency. Injection molding is commonly employed in the automotive, electronics, medical, packaging, and consumer goods industries. It is used to manufacture components such as automotive dashboards, electronic housings, medical devices, bottle caps, toys, and many other plastic products. The process allows for the efficient production of complex shapes, intricate details, and tight tolerances, making it an ideal choice for mass production.
Injection molding is used to make a vast array of plastic products that we encounter in our daily lives. It enables the production of various items, ranging from small and intricate parts to larger components. Some common products made through injection molding include plastic bottles, containers, lids, household appliances, automotive parts (such as interior trims and bumpers), electronic enclosures, medical devices, toys, and even intricate components used in aerospace and defense industries. The versatility of injection molding allows manufacturers to create products with different shapes, sizes, textures, and functionalities, meeting the diverse needs of numerous industries and consumers worldwide.
Injection molding plastic refers to the type of plastic material used in the injection molding process. It is a broad term that encompasses various types of thermoplastics, which are polymers that can be melted and reshaped multiple times without undergoing significant chemical changes. Common examples of injection molding plastics include polyethylene (PE), polypropylene (PP), polystyrene (PS), acrylonitrile butadiene styrene (ABS), polyvinyl chloride (PVC), and many others. These plastics possess different characteristics such as strength, flexibility, transparency, heat resistance, and chemical resistance. The choice of injection molding plastic depends on the desired properties of the final product, its intended application, and the manufacturing requirements.
Injection molding plays a crucial role in engineering, particularly in the field of manufacturing and product development. It is a widely used process that enables engineers to create complex plastic components with high precision and efficiency. In engineering, injection molding is employed to produce a wide range of parts used in various industries, including automotive, aerospace, electronics, medical devices, consumer goods, and more. The process allows engineers to transform design concepts into tangible products by injecting molten plastic into a mold, resulting in the replication of intricate details and the formation of precise shapes. Injection molding in engineering ensures the mass production of components with consistent quality, dimensional accuracy, and optimal mechanical properties, making it an essential technique in modern manufacturing processes.
Injection molding consists of four primary stages, each crucial to the overall process:
Clamping: The first stage involves securely closing the mold using a clamping unit. The purpose of this stage is to ensure that the mold remains tightly shut during the subsequent steps and that it can withstand the high pressure exerted during injection.
Injection: In this stage, the plastic material, usually in the form of pellets or granules, is melted and injected into the mold cavity. The molten plastic is forced into the mold under high pressure through a nozzle and runner system, filling the cavity completely.
Cooling: After the mold is filled, the molten plastic is allowed to cool and solidify. Cooling time varies depending on factors such as the size and thickness of the part, as well as the type of plastic used. Cooling is crucial to ensure that the part retains its shape and dimensional accuracy.
Ejection: Once the plastic has solidified, the mold opens, and the finished part is ejected from the cavity. Ejection can be facilitated by ejector pins, air blasts, or other mechanical methods. The cycle then repeats, and the mold is ready for the next injection.
These four stages are repeated continuously, enabling the efficient production of multiple plastic parts in a continuous cycle.
Molding is a manufacturing process that involves shaping a material into a specific form by using a mold. It is widely used in various industries to produce parts and products made from materials such as plastic, metal, glass, ceramics, and composites. The molding process typically involves heating the material to a molten or semi-molten state and then transferring it into a mold, where it solidifies and takes the desired shape.
There are several types of molding techniques, including:
Injection Molding: This process, as discussed earlier, involves injecting molten material into a mold cavity under high pressure. It is commonly used for producing plastic parts.
Blow Molding: In blow molding, a hollow tube of molten material, usually plastic, is formed and then inflated to conform to the shape of the mold. It is commonly used for producing bottles, containers, and other hollow objects.
Compression Molding: Compression molding involves placing a predetermined amount of material into a heated mold cavity and then compressing it under high pressure until it takes the desired shape. This method is often used for producing larger parts and products from materials like rubber, thermosetting plastics, and composites.
Rotational Molding: Rotational molding, also known as rotomolding, is a technique where a hollow mold is filled with powdered material, heated, and rotated slowly. The material melts and coats the inner surface of the mold, forming a solid product with even thickness. It is commonly used for producing large, seamless, and hollow objects such as tanks, playground equipment, and furniture.
These are just a few examples of molding processes, each with its own advantages and applications. The choice of molding method depends on factors such as the material being used, the complexity of the part, production volume, and desired characteristics of the final product.
Injection molding is a versatile manufacturing process that finds extensive application across a wide range of industries. Its primary use is in the production of plastic parts on a large scale. Injection molding enables the creation of intricate and complex shapes with high precision and repeatability. This process is employed in industries such as automotive, electronics, medical, consumer goods, packaging, and more. It is utilized to manufacture various components like housings, enclosures, connectors, gears, knobs, caps, and many other plastic products. The ability to produce parts with consistent quality, dimensional accuracy, and excellent surface finish makes injection molding an ideal choice for mass production, reducing costs and increasing efficiency.
Injection molds are essential tools in the injection molding process. They determine the shape, form, and specifications of the final plastic part. Here are five commonly used types of injection molds:
Two-Plate Mold: This is the simplest and most commonly used injection mold. It consists of two plates, the cavity plate and the core plate, which separate to allow the ejection of the molded part. Two-plate molds are relatively easy to design, construct, and maintain, making them cost-effective for producing simpler parts.
Three-Plate Mold: A three-plate mold includes an additional plate, known as the stripper plate or the moving plate, between the cavity and core plates. The stripper plate is used to separate the molded part from the runner system, facilitating the ejection process. Three-plate molds are useful for parts with complex geometries or when automatic part removal is required.
Hot Runner Mold: In a hot runner mold, the runner system (the channels through which the molten plastic flows) remains hot even after the injection molding cycle. This eliminates the need for re-solidification of the runners, reducing material waste and improving cycle time. Hot runner molds are commonly used for high-volume production of parts with multiple cavities or complex geometries.
Stack Mold: A stack mold consists of multiple mold layers or levels, allowing for the simultaneous molding of multiple parts in a single molding cycle. This design significantly increases productivity and reduces production costs. Stack molds are often employed in applications where high production volumes and space optimization are critical.
Insert Mold: In insert molding, pre-formed inserts or components (such as metal pins, threaded inserts, or electronic circuits) are placed into the mold cavity before injection. The molten plastic material then encapsulates the inserts during the molding process, resulting in a single, integrated part. Insert molding is beneficial for enhancing component strength, reducing assembly steps, and creating complex parts with added functionality.
These are just a few examples of the different types of injection molds. The selection of mold type depends on factors such as the complexity of the part, desired production volume, material characteristics, and specific requirements of the application.
An injection mold consists of three primary parts that work together to shape the molten plastic material into the desired form:
Cavity: The cavity is the part of the mold that defines the outer shape and features of the final product. It forms the negative space into which the molten plastic is injected, solidifies, and takes the shape of the intended part. The cavity is typically created by machining or EDM (Electrical Discharge Machining) to precise specifications and surface finish requirements.
Core: The core complements the cavity by creating the internal features of the molded part. It forms the positive space within the mold and is designed to fit precisely inside the cavity. The molten plastic fills the space between the cavity and core, taking the desired shape and forming the internal details of the part. The core is usually positioned and aligned with the cavity to ensure proper molding.
Mold Base: The mold base is the foundation of the injection mold and holds all the components together. It provides support and rigidity to the mold during the injection process. The mold base incorporates features such as support pillars, guide pins, cooling channels, and the system for attaching the mold to the injection molding machine. The mold base is typically made of high-quality steel or aluminum to withstand the high pressures and temperatures involved in injection molding.
These three main parts, the cavity, core, and mold base, are carefully designed and precision-machined to create a mold that enables the production of high-quality plastic parts with accuracy and repeatability.
Injection speed in injection molding is typically measured and expressed in millimeters per second (mm/s) or inches per second (in/s). It represents the velocity at which the molten plastic material is injected into the mold cavity during the injection stage. The injection speed is a critical parameter that affects the filling of the mold, the flow characteristics of the plastic, and the final part's quality. The appropriate injection speed is determined based on factors such as the material being used, the complexity of the part's geometry, and the desired properties of the finished product. By controlling the injection speed, manufacturers can optimize the molding process to achieve consistent and defect-free parts.
Injection molding is compatible with a wide range of plastic materials, allowing for versatility in producing different types of parts and products. The choice of plastic material in injection molding depends on factors such as the required mechanical properties, chemical resistance, heat resistance, transparency, and cost considerations. Some commonly used types of plastics in injection molding include:
Polyethylene (PE): PE is a versatile thermoplastic known for its toughness, flexibility, and chemical resistance. It is commonly used in applications such as packaging, containers, and automotive components.
Polypropylene (PP): PP is a lightweight thermoplastic that offers excellent chemical resistance, stiffness, and impact strength. It is widely used in automotive parts, household appliances, and consumer products.
Polystyrene (PS): PS is a rigid, transparent or opaque thermoplastic with good electrical insulation properties. It is used in packaging, consumer goods, and disposable products.
Acrylonitrile Butadiene Styrene (ABS): ABS is a tough and impact-resistant thermoplastic with good dimensional stability. It is commonly found in automotive components, electronics, and consumer goods.
Polyvinyl Chloride (PVC): PVC is a versatile thermoplastic known for its durability, chemical resistance, and low cost. It is used in various applications, including pipes, cables, flooring, and medical devices.
These are just a few examples, and there are numerous other plastic materials used in injection molding, each with its unique properties and applications. The selection of the plastic material depends on the specific requirements of the part, including its intended use, desired performance characteristics, and regulatory compliance.
Injection capacity refers to the maximum amount of molten plastic material that can be injected into the mold during a single injection cycle. It is typically measured in terms of the volume of material, such as cubic centimeters (cc) or ounces (oz). The injection capacity is determined by the design and specifications of the injection molding machine, specifically the size and configuration of the injection unit. It plays a crucial role in determining the size and weight of the plastic part that can be produced. Manufacturers need to consider the injection capacity when selecting a suitable injection molding machine for their production needs to ensure it can accommodate the required volume of plastic material.
The injection speed in injection molding is typically controlled and adjusted based on the specific requirements of the part being produced. While there is no specific formula for calculating injection speed, it is typically determined through process optimization and experience. Injection speed is influenced by various factors, including the material being used, part geometry, mold design, and machine capabilities. Manufacturers often rely on the expertise of process engineers to determine the optimal injection speed for a given application. By adjusting machine settings, such as screw speed and hydraulic pressure, they can control the injection speed and achieve desired filling, part quality, and cycle times.
Injection rate, also known as fill rate, refers to the speed at which the molten plastic material is injected into the mold cavity during the injection molding process. It is typically expressed in cubic centimeters per second (cc/s) or inches per second (in/s). The injection rate affects the flow behavior of the plastic material within the mold cavity, influencing the filling pattern, material distribution, and overall part quality. The injection rate is controlled by adjusting the machine settings, such as screw speed, hydraulic pressure, and shot size. By optimizing the injection rate, manufacturers can achieve uniform filling, minimize part defects like voids or short shots, and ensure consistent part dimensions. The appropriate injection rate varies depending on the specific material being used, part design, mold complexity, and desired production requirements.