January 2nd, 2018
An overview of 3D Printing & CNC, and how they can be utilized together to achieve superior results.
SUBTRACTIVE MANUFACTURING (CNC MACHINING) PROCESS OVERVIEW

3D printing, printform
Subtractive manufacturing (or CNC) is the process of starting with more material that is needed in sheet, rod or block form, and selectively removing material that is not required until the final shape emerges. This process is better understood by using the marble sculptures of the famous artist Michelangelo as an example. When asked by the Pope how he made his statue of David so beautifully lifelike, he said: “I simply remove everything that doesn’t look like David”. This is the basic principle of subtractive manufacturing; start with too much and then remove what you don’t need.
APPLICATIONS
Subtractive manufacturing has been used for almost everything historically, going all the way back to humans’ earliest tools being shaped from organic materials and items found in nature (e.g. sticks and stones). From the simple to the impressively complex, subtractive manufacturing has been the worldwide standard for customized one-offs and mass-produced products and tools alike.
ADDITIVE MANUFACTURING (3D PRINTING) PROCESS OVERVIEW
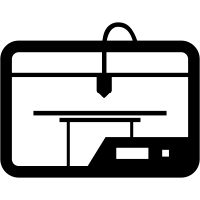
Additive manufacturing, on the other side of the spectrum, is the process of generating 3D objects by adding only what is needed, one layer at a time, along with any support material required. The most common way to do this is by placing very thin layers of material on top of one another to stack up and form the final object, like layers of a cake. This process dramatically reduces the time, cost and waste produced from its subtractive counterpart, and allows a much more efficient production process.
APPLICATIONS
Additive processes have in the past been too costly for mass-produced products, but have still found their way into the production process, mostly in prototyping and complex jig and fixture creation. They have been frequently used for some time now, dating back to the late 80’s when SLA & FDM were first introduced to prototype and test new product designs. For companies like Nike, the production of ‘one of a kind’ test products is one cost-effective use of additive manufacturing.
COMBINING TWO QUALIFIED TECHNOLOGIES
When the two are used simultaneously, the results can bring previously untold efficiency to the product development process. Examples include near net shape printing, part assembly, fixture printing, and comparison studies. Engineers that are experienced in both of these manufacturing techniques can bring new and exciting efficiency to their teams’ development process.

Original component (made up of several parts assembled / welded together) and the two resulting 3D printed parts that are purpose-built and designed exclusively for the application without regard to traditional manufacturing concessions.
3D Printed fixture used in assembly minimizing human error and misplaced hardware inserts in the final component.
About the Author: Bill Artley is the Vice President of Operations at PrintForm and has written many articles & white papers on product development, sourcing, additive manufacturing, and materials. He is a contributing author and peer reviewer of The 3D Handbook (http://a.co/h9fL1b5), a top 10 Amazon Best Seller in its category.