PrintForm – Your Automotive Machining Partner
At PrintForm, we overcome the challenges of injection molding by assisting in the design and manufacture of molds that will produce high-precision, geometrically complex molded parts in high volumes. Our injection molding capabilities include cleanroom molding, over-molding, insert molding, and in-mold labeling. We can produce multi-component parts with Class A surfaces, complex geometries, undercuts, and thin walls and easily uphold tolerances as small as ±0.001 inches.
By partnering with us for their injection molding needs, automotive industry customers benefit from our:
- Rigorous materials management program with special attention to humidity, material density, and mix ratios.
- Bi-hourly internal inspections that ensure parts meet precise function, strength, durability, and color specifications.
- Adherence to ISO 9001 and ISO 13485 standards
Our best-in-class engineering and manufacturing capabilities have earned us a reputation as a trusted partner for customers across a wide range of industries, including automotive, consumer, medical, and electrical. For additional information on our injection molding capabilities and how we serve the automotive industry, contact us orrequest a quote today.
PrintForm is helping to accelerate vehicle design by providing prototypes and production parts for a wide variety of applications. Harness the power of traditional manufacturing processes like CNC machining and injection molding, along with modern additive manufacturing processes that allow complexities unachievable through traditional means. Whether the need is to improve fuel economy, eliminate tooling costs, or optimize part count to weight ratios, PrintForm is here to serve our automotive customers and help them achieve their goals.
Whether the need is to improve fuel economy, eliminate tooling costs, or optimize part count to weight ratios, PrintForm is here to serve our automotive customers and help them achieve their goals.
Road Ready Performance
For automotive parts and products machining, PrintForm offers the highest degree of service with a basis of 20+ years experience serving the automotive industry. Our automotive machine shop and experts deliver confidence. We have perfected the art of producing large component volumes with complete JIT reliability, backed by the quality and long-term reliability our customers expect.
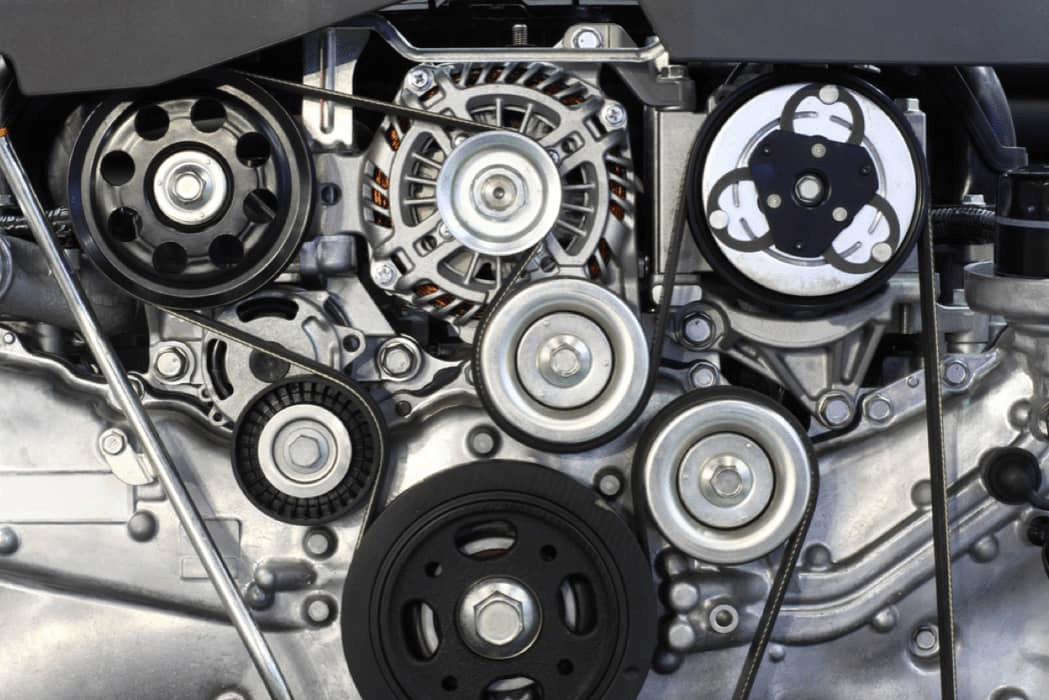
Commonly Machined Automotive Components
- Titanium Valve Keepers
- Brake System Components
- Dowel Pins
- Splined Shafts
- Bushings
- Timing Covers
- Valve Retainers
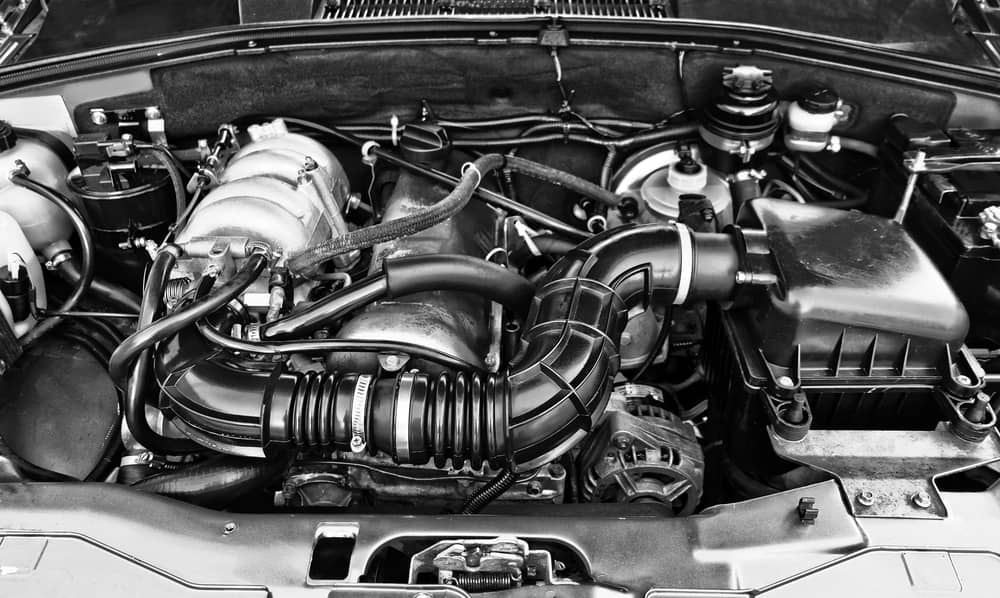
Automotive Machining Materials:
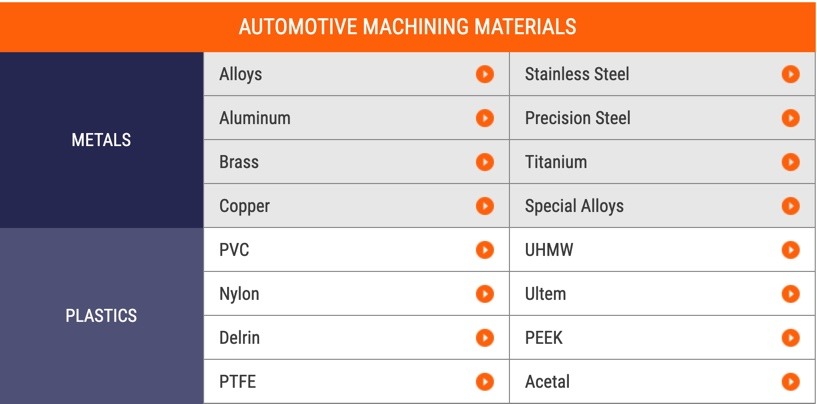
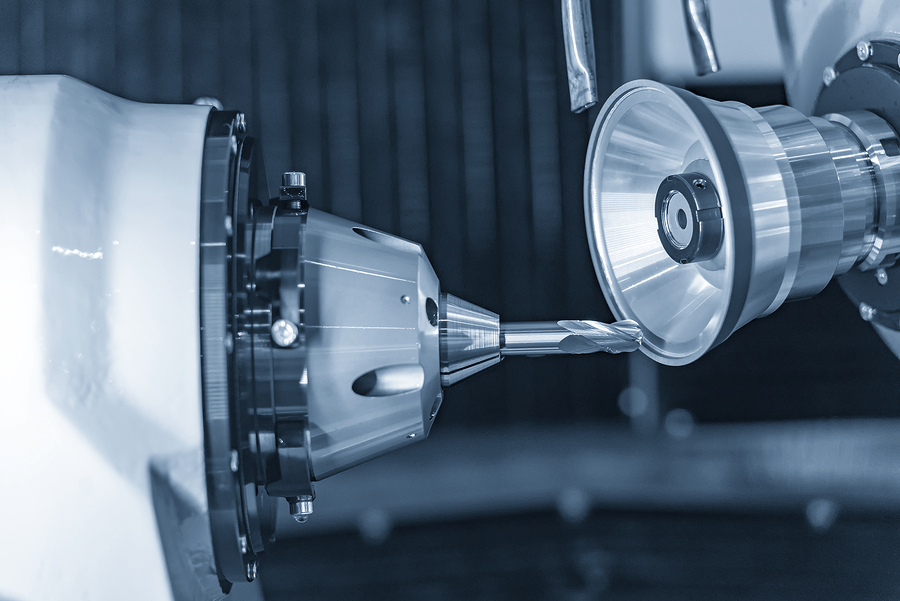
NC Machining Enhances Auto Manufacturing Processes and Quality
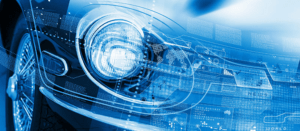
COMMON AUTOMOTIVE APPLICATIONS
Automotive manufacturers are always looking for ways to innovate, create more efficiency, and improve their products. Here’s how we can help you:
- Engine parts
- Interior components
- Hinges and Brackets
- Battery housings and compartments
CNC machining car parts
Engines
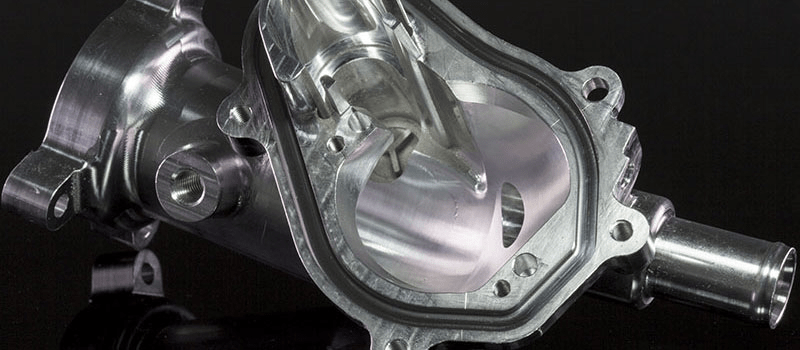
CNC machining can be used to create several important components of a car’s combustion engine. For example, a large aluminum block can be machined into an engine block (or cylinder block), the metal structure that comprises an engine’s cylinders where moving pistons travel up and down.
Although programming the CNC machine is a time-consuming process that requires a high level of skill, the machine can once prepared, carry out its instructions without assistance. This means multiple engine blocks can be machined in succession without a significant increase in labor.
Cylinder heads, parts that enclose the cylinders above the cylinder block, are also commonly produced using CNC machining techniques.
Lighting
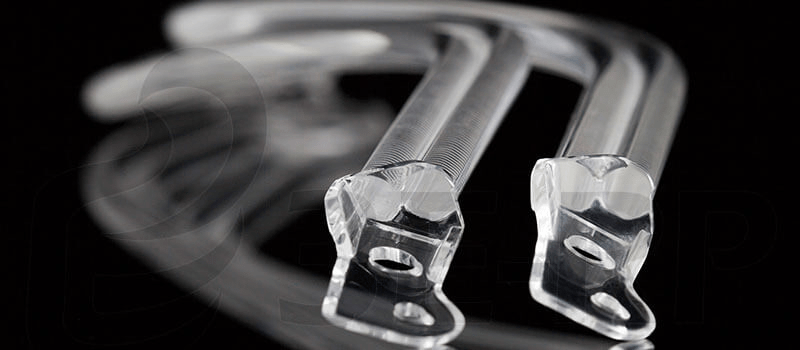
The machining of aluminum is one of the most important applications of CNC technology in the automotive industry, but materials such as acrylic glass or Poly(methyl methacrylate) (PMMA) can be used to make other important components.
Poly(methyl methacrylate) (PMMA) commonly used as a shatter-resistant alternative to glass and can be made into windows, transparent shields, fish tanks, and other objects.
CNC Machined Car Parts
1.Engines
CNC machining can be used to create a few key components of a car’s combustion engine. For instance, a large aluminum block can be machined into a cylinder block. This is the metal structure that contains an engine’s cylinders where moving pistons travel up and down.
Through programming the CNC machine is a time-consuming process that requires a high level of skill, once prepared the machine can carry out its instructions without any assistance. Therefore, numerous engine blocks can be machined in sequence without a significant increase in labor.
Engine parts also generally produced using CNC machining techniques include:
- Cylinder heads
- Parts that enclose the cylinders above the cylinder block
2.Lighting
In the automotive industry, the machining of aluminum is one of the most important applications of CNC machining. However, materials such as acrylic glass or Poly (methyl methacrylate) (PMMA) can be used to make other significant components.
Machining PMMA enables manufacturers to produce lighting for a vehicle, both its headlights and interior lighting. Even though these acrylic pieces need grinding and polishing after the CNC machining, the entire process is still quite fast. Therefore, allowing auto manufacturers to prototype new light fixtures for their cars quite quickly.
Commonly used as a shatter-resistant alternative to glass, PMMA can also be used for:
- Fish tanks
- Transparent shields
- Windows
3.Other parts
CNC machining is also used to produce a vast range of other car parts, such as:
- Fluid system components
- Exhaust parts
- Bushings
- Suspension components
- Valve retainers
- Carburetor housings
In addition, CNC machining is particularly useful for customizing vehicles and their specific components, since CAD allows for the quick alteration of part designs.
Advantages of CNC machining car parts
- Production speed
- Accuracy & precision
- Repeatability
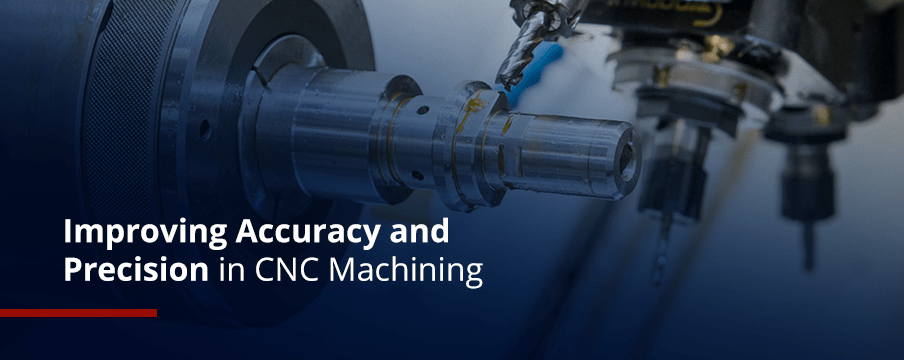
Injection Molding
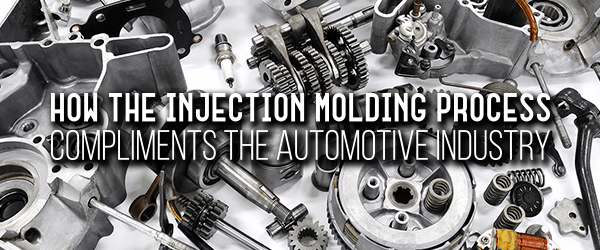
Applications of Plastic Injection Molding in the Automotive Industry
In the automotive industry, the plastic injection molding process is used to manufacture a wide range of parts, including:
- Panel components such as lenses, bezels, knobs, assemblies, door handles and handle components, housings, and sunroof parts.
- Under-the-hood components such as oil pans, fans and fan shrouds, HVAC kinematics, and radiator end tanks.
- Exterior components such as fenders, grilles, bumpers, door panels, floor rails, light housings, skid plates, and wheel trims.
- Interior components such as air vents, glove compartments, door handles, dashboard faceplates, and instrumentation parts.
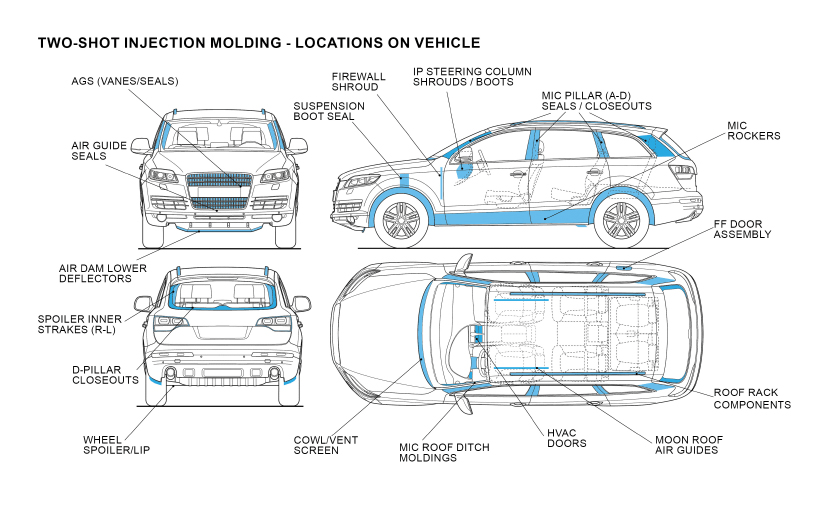
How to Choose the Right Material for Automotive Injection Molding Operations?
When selecting a material for an injection molding operation, there are several factors to keep in mind, including:
- Tensile Strength
- Flexural Modulus of Elasticity (FME)
- Izod Impact
- Heat Deflection Temperature (HDT)
- Water Absorption
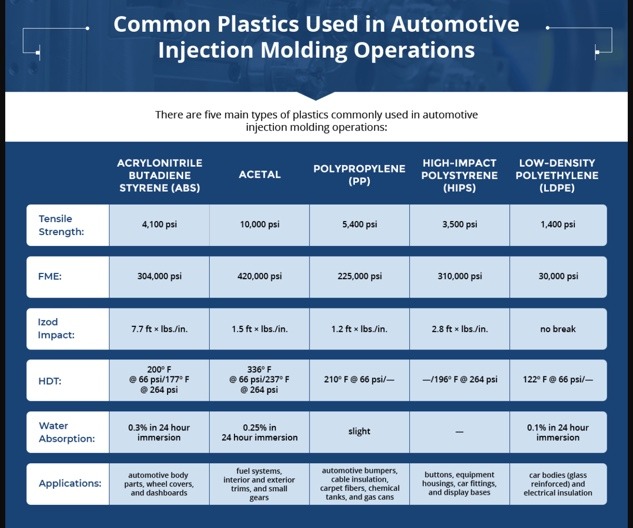
Advantages of Automotive Injection Molding
When used for the manufacture of automotive parts and products, injection molding offers several advantages, including:
- Cost-effectiveness (especially for high-volume production)
- Process repeatability and product consistency
- Operator and user safety
- Lightweight alternative to metal components
Submit Program Details